Behind the Scenes: Crafting Custom Uniforms
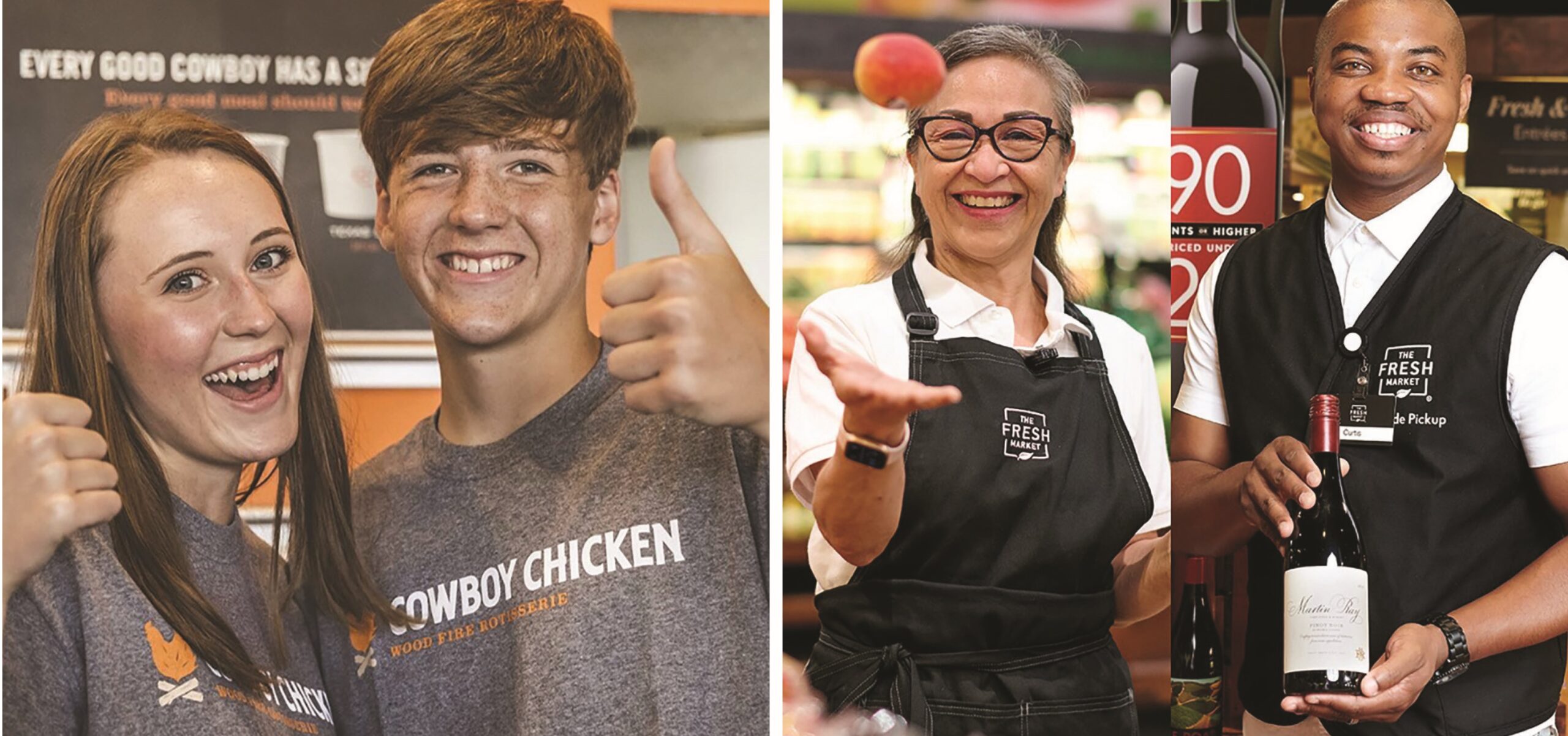
At Threads Uniform Agency, we don’t just deliver uniforms. We weave stories of identity and functionality into every stitch. Helping make this possible are team members like Isabel Edmonds, Brand Developer, and Naomi Sasaki-Whalen, Senior Product Development Manager, who bring attention to detail, personalization and customization to every order.
Step 1: Insightful Consultation and Discovery
With a keen eye for detail and a knack for understanding your brand’s essence, Isabel delves deep into your aspirations, as well as industry nuances. From deciphering brand standards to immersing herself in the ethos of your business, she crafts uniform programs that are perfectly designed for client needs – considering fabric type, how it needs to function, cost and timelines. Whether you’re looking for durability, comfort, or specific performance features, we have a wide range of options to choose from. From classic cotton blends to high-tech moisture-wicking fabrics, we ensure that your uniforms not only look great but also perform under pressure. So whether a client needs a subtle uniform refinement or a bold reimagining, Isabel acts as a guide through the labyrinth of design possibilities. And that’s true of our entire team at Threads, whether you’re a small local business or a large corporation, we’ll work closely with you to conceptualize a uniform program that is perfectly custom.
Step 2: A Customized Fit
Transition seamlessly into the realm of fit, color and brand consistency with Isabel’s counterpart, Naomi. Once the design concept is approved, we move on to fit. Threads has engaged experts to develop fit pattern packages for sizes XXS through 8XL that are exclusive to Threads, so you can count on the perfect fit, no matter size, every time. Naomi and team are key to this process of ensuring every thread aligns with your vision – and is a big reason supplier and vendor relationships are also critical. Threads’ ability to exceed expectations can’t happen without a proven, quality network we all can trust.
Step 3: Prototyping and Feedback
Attention to detail doesn’t end with design and fabric selection. Prototyping and creating approval samples before full orders are made is critical to making sure color, fit, logo placement, and so on are exactly as they should be. The work to create detailed technical requirements is meticulous and is a very collaborative process. A recent example is for a grocery retailer looking to replace their safety vests for team members working to collect carts in their parking lots. There is a reflectivity requirement for these items, and Threads is putting in the work to identify the perfect recipe to deliver by testing and retesting samples of fabric to meet our clients’ exact requirements.
Step 4: Production and Quality Control
Once samples are approved, we move into full-scale production where we ensure that each uniform is meticulously crafted to the highest standards. Throughout the production process, we conduct quality control checks to ensure that every garment meets our strict quality criteria. And we stay on top of your orders to deliver quality products, on time, every time.
Beyond Delivery
As your trusted partners, our journey doesn’t end with delivery; it’s just the beginning of an ongoing relationship. Our Sales and Client Services representatives stand ready to support you at every turn, ensuring we are poised for action if needs change or new needs emerge. Whether it’s sizing guidance, reorders, or beyond, our dedicated team is here to empower your journey every step of the way.
Contact us today to embark on a journey where every uniform tells a story, and every stitch weaves a legacy of excellence!
Want to see Threads in action? Explore our work and discover how we’re delighting clients one thread at a time!